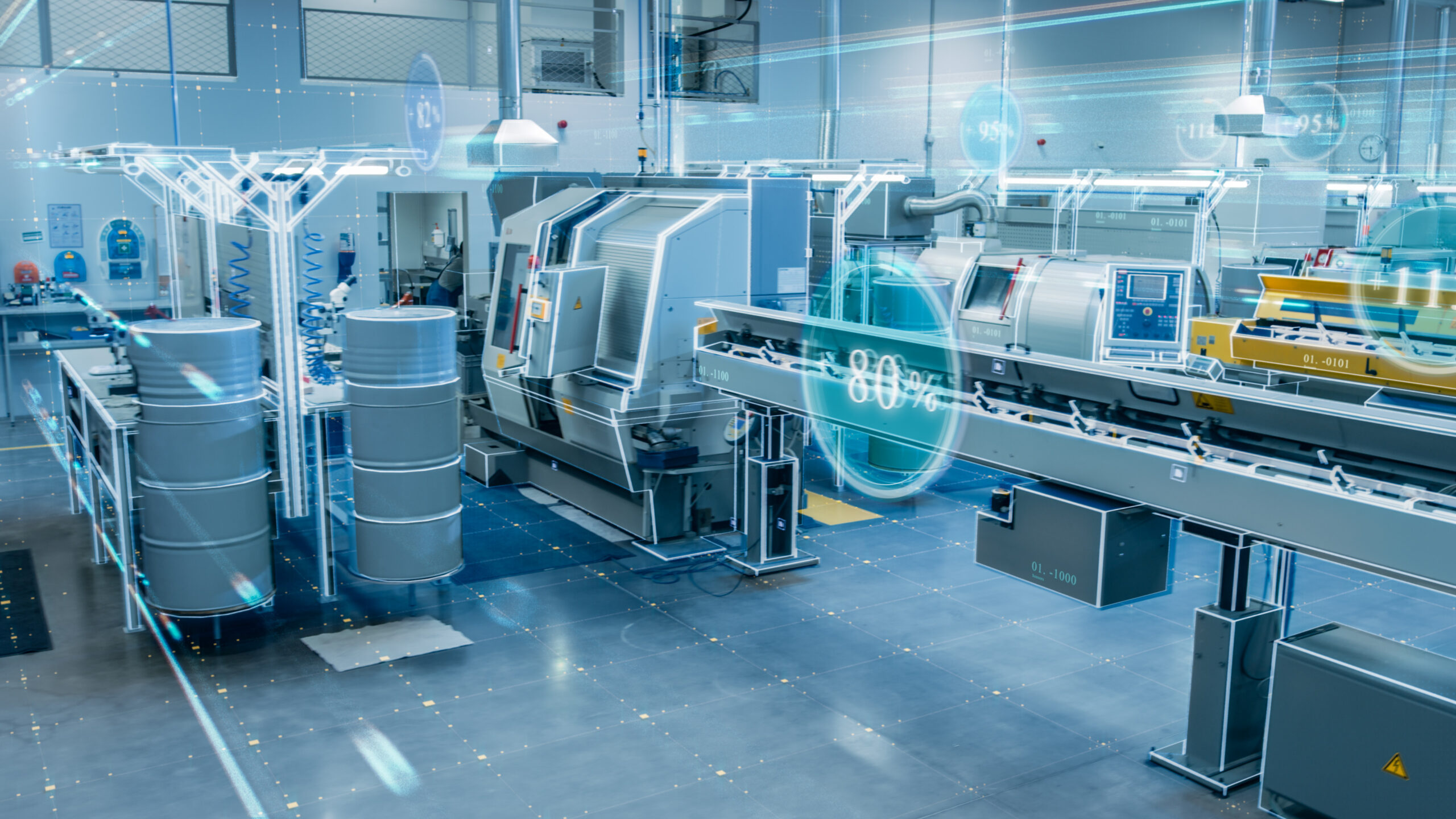
In a remarkable leap forward for the manufacturing industry, cutting-edge advancements in Manufacturing Execution System (MES) technology have sparked a revolution in the way factories and production lines operate. As companies strive to embrace the principles of Industry 4.0, MES has emerged as a vital component, enabling seamless integration, real-time data analysis, and enhanced productivity.
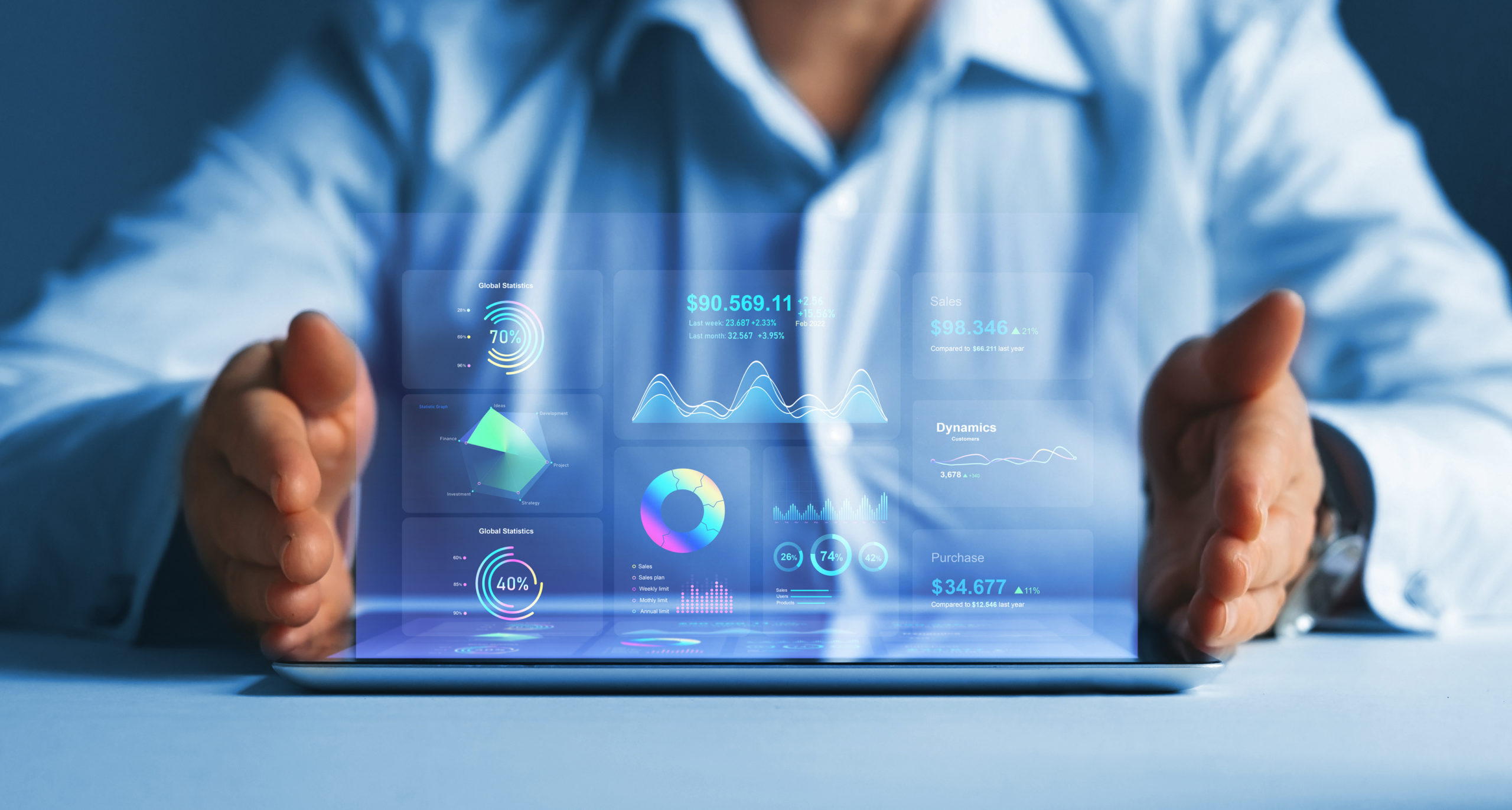
Traditionally, MES has played a crucial role in streamlining manufacturing operations by connecting and coordinating various aspects of production, including planning, scheduling, inventory management, quality control, and data collection. However, recent developments have propelled MES into a new era of efficiency and automation.
One of the key breakthroughs is the integration of MES with advanced technologies such as the Internet of Things (IoT), artificial intelligence (AI), and machine learning (ML). By connecting machines, sensors, and devices throughout the production process, MES now facilitates the collection and analysis of vast amounts of real-time data. This data-driven approach empowers manufacturers to optimize their operations, identify bottlenecks, predict maintenance requirements, and make data-informed decisions promptly.
The synergy between MES and AI/ML technologies has also enabled predictive analytics, allowing manufacturers to anticipate and prevent production issues before they occur. By leveraging historical data, algorithms can forecast potential equipment failures, identify quality deviations, and optimize production parameters to enhance overall efficiency. This proactive approach reduces downtime, minimizes waste, and enhances product quality, providing a significant competitive advantage.
Another notable development is the rise of cloud-based MES solutions, which have revolutionized accessibility, scalability, and collaboration in the manufacturing sector. Cloud-based MES allows for centralized management of multiple production sites, enabling seamless data sharing and real-time monitoring across geographically dispersed locations. Furthermore, cloud platforms offer enhanced flexibility, allowing manufacturers to quickly adapt to changing market demands, scale their operations, and implement updates or new functionalities without extensive infrastructure investments.
Moreover, the integration of MES with other systems, such as Enterprise Resource Planning (ERP) and Customer Relationship Management (CRM), has facilitated end-to-end visibility and connectivity across the entire supply chain. This integration enables manufacturers to gain insights into customer demands, synchronize production with orders, and optimize inventory levels, ultimately improving customer satisfaction and reducing lead times.
As MES continues to evolve, its impact on the manufacturing industry is profound. By embracing the power of data, connectivity, and automation, companies can transform their operations, increase productivity, and unlock new avenues for growth. MES is no longer just a supporting technology; it has become the cornerstone of Industry 4.0, reshaping the future of manufacturing.
With MES at the forefront of this transformation, manufacturers worldwide are poised to revolutionize their production processes, leverage data-driven insights, and propel their businesses to new heights of success in the dynamic landscape of Industry 4.0.
MES software plays a vital role in modern manufacturing by providing real-time visibility, optimizing resource management, ensuring quality control, and fostering effective communication. Its implementation enables manufacturers to streamline their operations, increase productivity, reduce costs, and remain competitive in today’s dynamic business environment. As manufacturing processes continue to evolve and become more complex, MES software will continue to be a crucial tool for driving operational excellence and achieving sustainable growth.
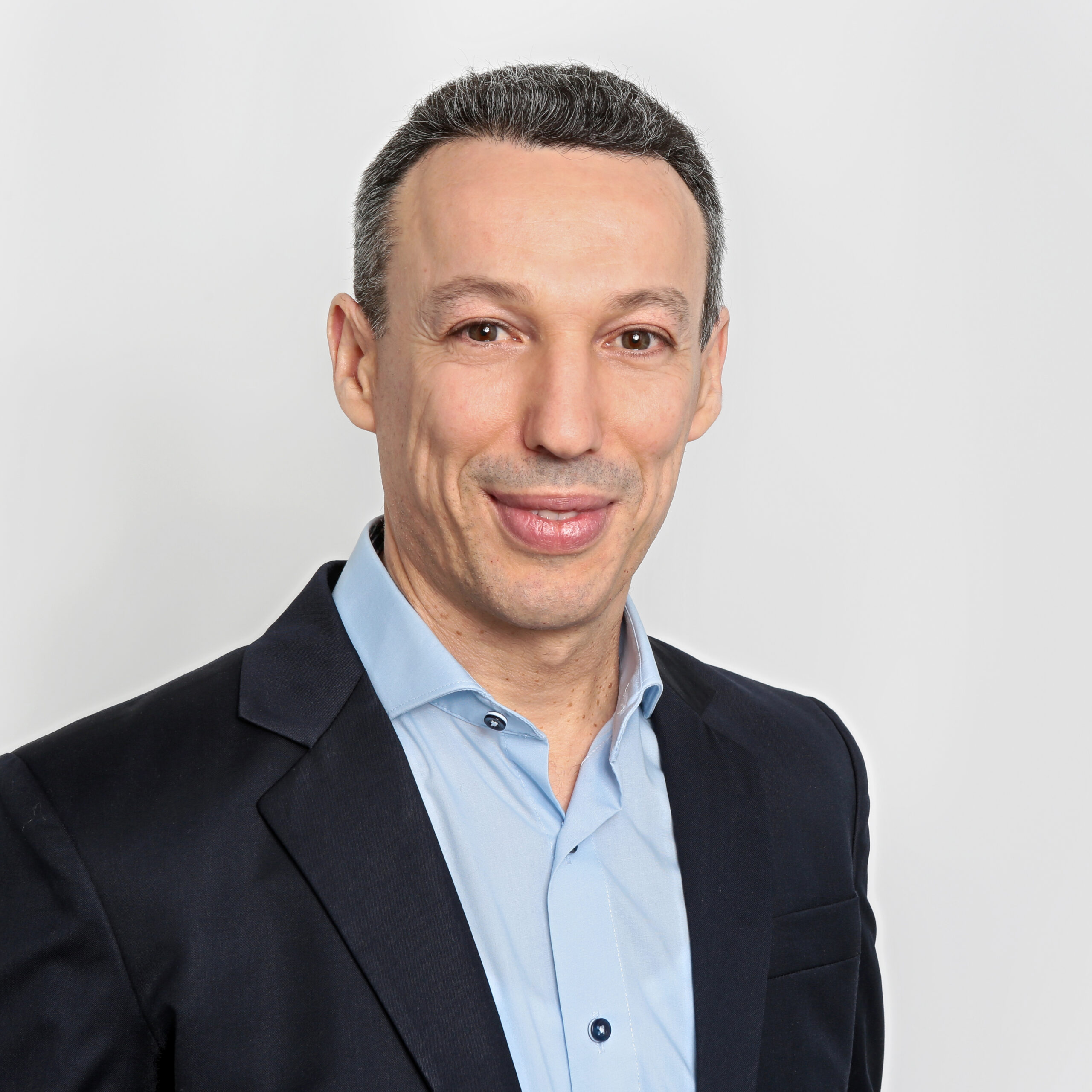
Dr. Mourad Chouikha
CASE Deutschland GmbH,
Founder & CEO
Tel: +49 (0)531 237 68 8-02
E-Mail: m.chouikha@case-deutschland.de